This comprehensive wastewater pump troubleshooting guide addresses frequent failures in wastewater treatment systems, including centrifugal pump cavitation remedies, submersible sewage pump failures, and chemical dosing pump issues. It provides detailed symptoms, causes, technical explanations, remedies, and prevention strategies to help operators and engineers minimize downtime and ensure efficient operation.
Table of Contents
- Cavitation
- Clogging and Blockages
- Overheating
- Leaks
- Vibration and Unusual Noises
- Pulsation
- Seal Failures
- Motor Failure
- Float Switch Malfunction
- Reduced Flow or No Flow
- Impeller Damage/Wear
- Air Binding/Air Locks
- Electrical Failures
- Bearing Failure
- Corrosion
- Pump Won't Turn Off
- High-Level Alarm Sounding
- Bad Smells
- Inconsistent Dosing/Flow in Chemical Pumps
- Vapor Lock in Chemical Dosing Pumps
- Diaphragm Failure in Dosing Pumps
- Calibration and Control Issues
- Siphoning/Overdosing in Chemical Pumps
- Acronyms
- FAQ Section
- Bibliography
1. Cavitation
Symptoms: Rumbling or crackling noises, vibration, reduced
flow/pressure, fluctuating discharge, pitting/erosion on impeller or casing, fluctuating
motor amp draw.
Causes: Insufficient NPSHa due to high fluid temperature, low suction
pressure, restricted inlet, or high vapor pressure fluids. Common in submersible sewage
pumps to varying degrees.
Technical Explanation: Cavitation occurs when local pressure drops below
the fluid's vapor pressure, forming vapor bubbles that collapse implosively upon entering
higher-pressure zones, causing shock waves (up to 10,000 psi) that erode metal surfaces and
reduce efficiency by 10-20%. NPSHa must exceed NPSHr by 2-3 ft; calculate NPSHa = atmospheric
pressure + static head - vapor pressure - friction losses. In wastewater, solids exacerbate
damage.
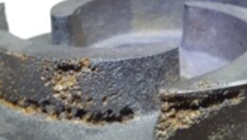
- Calculate NPSHa vs. NPSHr; increase suction head (e.g., lower pump or raise liquid level).
- Reduce pump speed via VFD or trim impeller diameter to lower NPSHr.
- Clear suction restrictions; use larger suction piping (min. 1.5x pump inlet).
- Install inductors or boost pumps for low-NPSH systems.
Prevention: Design systems with NPSHa margin of 20-30%; monitor suction pressure with gauges; use cavitation-resistant materials like stainless steel or hard coatings.
2. Clogging and Blockages
Symptoms: Sudden pressure spikes, reduced or no flow, pump shutdowns,
increased amp draw, backups in toilets/sewage lines.
Causes: Accumulation of solids, rags, wipes, grease, debris, or foreign
objects in impeller, volute, or pipes. Prevalent in sewage and grinder pumps handling 2
- 10% solids.
Technical Explanation: Blockages increase hydraulic resistance, shifting
operating point left on the pump curve, raising head and power draw while dropping efficiency.
In non-clog impellers, rags can wrap around shafts; grinder pumps may fail if blades dull.
Viscosity >1,000 cP in sludge worsens this.

- Isolate and de-energize pump; remove and inspect impeller/discharge pipe; clear with brushes, snakes, or high-pressure jets.
- For grinder pumps, sharpen/replace macerating blades.
- Use borescopes for internal inspection without full disassembly.
Prevention: Install upstream screens or macerator/grinder; educate on proper waste disposal (no wipes/flushables); schedule monthly inspections; use non-clog or vortex impellers for high-solids applications.
3. Overheating
Symptoms: Hot motor/bearings (>80°C / 176°F), thermal overload
trips, reduced performance, burnt smell, seal failures.
Causes: Dry running, overload from blockages, low coolant levels, poor
ventilation, or high ambient temperatures. Common in submersible pumps with low water
levels.
Technical Explanation: Heat buildup from friction (bearings/seals) or electrical
resistance exceeds dissipation, degrading lubrication (viscosity drops 50% per 10°C / 18°F
rise) and causing thermal expansion/misalignment. In motors, insulation class (e.g., Class
F: 155°C / 311°F limit) is exceeded, leading to winding failure. Wastewater solids can block
cooling paths.
- Shut down and cool; check/add fluid levels for cooling; clean vents/motor fins.
- Verify load vs. rating (use amp meter; should be < nameplate FLA).
- Inspect for blockages causing overload; recalibrate VFDs.
Prevention: Install thermal sensors/protectors; ensure submergence (min. 1 ft above pump for submersibles); use oil-filled motors for better heat transfer; monitor with IR thermography.
Motor Insulation Class | Temperature Limit (°C / °F) | Typical Applications |
---|---|---|
Class F | 155 / 311 | Standard wastewater pumps |
Class H | 180 / 356 | High-temperature environments |
4. Leaks
Symptoms: Fluid seepage at seals, joints, or casing; reduced pressure;
contamination; electrical hazards.
Causes: Worn/damaged seals, cracked pipes/valves, improper assembly, or
corrosion. In chemical pumps, aggressive pH <7 attacks materials.
Technical Explanation: Mechanical seals fail from dry running (face scoring)
or misalignment (radial runout >0.002 in.); gaskets degrade under pressure cycles. Leakage
reduces volumetric efficiency (up to 15% loss) and risks short circuits in submersibles.
- De-energize; inspect/replace seals (e.g., switch to silicon carbide faces for abrasives).
- Tighten connections; repair cracks with epoxy or replace sections.
- For housing leaks, pressure test (up to 1.5x operating pressure).
Prevention: Use compatible materials (e.g., Viton seals for chemicals); implement double seals with barrier fluid; routine leak detection with ultrasonic tools.
5. Vibration and Unusual Noises
Symptoms: Excessive shaking, banging, rattling; noise levels >85 dB;
alignment issues; premature wear.
Causes: Misalignment, imbalance, cavitation, loose parts, worn
bearings, or improperly secured pipes. Banging from check valve slam.
Technical Explanation: Vibration (measured in mils or mm/s RMS) excites
natural frequencies, causing fatigue (e.g., shaft deflection >0.001 in./in.). ISO 10816 standards
classify severity; wastewater abrasives accelerate bearing wear (L10 life <10,000 hrs.
if untreated).
- Use vibration analyzers (e.g., FFT for frequency peaks); balance impellers dynamically.
- Realign shafts (laser alignment to <0.002 in.); secure mountings/pipes.
- Replace worn bearings or valves (e.g., soft-close check valves).
Prevention: Baseline vibration monitoring; use flexible couplings; isolate with dampers; annual alignment checks.
ISO 10816 Severity Class | Velocity (mm/s RMS) | Condition |
---|---|---|
Good | <2.3 | Normal operation |
Satisfactory | 2.3-4.5 | Monitor |
Unsatisfactory | 4.5-7.1 | Alert |
Unacceptable | >7.1 | Shutdown |
6. Pulsation
Symptoms: Uneven flow/pressure fluctuations; pipe hammering; inaccurate
metering in chemical pumps.
Causes: Inherent in positive displacement pumps (e.g., reciprocating
stroke); air entrapment; worn rotors in progressive cavity.
Technical Explanation: Pulsation amplitude can reach 20-50% of mean pressure,
causing fatigue in pipes (per ASME B31.3). Dampeners absorb peaks by gas compression (e.g.,
bladder type with 80% pre-charge).
- Install pulsation dampeners on discharge; bleed air from lines.
- Use VFDs for smoother speed control; select low-pulsation designs like peristaltic.
Prevention: Size dampeners (volume = stroke volume x factor); use multi-cylinder pumps; regular air bleed protocols.
7. Seal Failures
Symptoms: Leaks around shaft; reduced pressure; fluid contamination;
overheating.
Causes: Abrasives wearing faces, improper lubrication, misalignment,
chemical attack, or dry running.
Technical Explanation: Seals operate on a thin fluid film (1-3 microns);
failure modes include cracking (thermal shock) or extrusion (high pressure >500 psi).
MTBF <1 year in abrasive sludge without flushing.
- Select compatible seals (e.g., tungsten carbide for solids); flush with clean fluid (API Plan 32).
- Schedule inspections; correct alignment/balance.
Prevention: Use barrier systems or cartridge seals; monitor flush pressure (5-10 psi above seal chamber); predictive maintenance with vibration/seal face temp sensors.
8. Motor Failure
Symptoms: Won't start, burnout, unusual smells, high amp draw, trips.
Causes: Electrical faults, overload, water ingress in submersibles, or
phase imbalance.
Technical Explanation: Overload heats windings (I²R losses); insulation
breakdown at > Class H limit (180°C / 356°F). Voltage drops >10% reduce torque by 19%.
- Test windings with megohmmeter (>1 MΩ); repair/replace.
- Check power supply/phases; reset overloads.
Prevention: Use soft starters; monitor voltage/amps; seal against moisture (IP68 for submersibles).
9. Float Switch Malfunction
Symptoms: Pump won't activate/deactivate; overflows or dry running.
Causes: Debris tangling, misalignment, wear, or electrical failure.
Technical Explanation: Mercury or mechanical switches fail from arcing or
corrosion; setpoint drift in varying densities.
- Clean/adjust float; test continuity; replace if faulty.
Prevention: Use ultrasonic level sensors as backup; regular testing.
10. Reduced Flow or No Flow
Symptoms: Low output, high head, inefficiency.
Causes: Blockages, worn impeller, air locks, insufficient NPSHa.
Technical Explanation: Operating point shifts right on curve; efficiency
drops <50%.
- Clear lines; replace impeller; vent air.
Prevention: Flow meters; proper priming.
11. Impeller Damage/Wear
Symptoms: Reduced flow, vibration, noise.
Causes: Abrasives, cavitation, corrosion.
Technical Explanation: Erosion rates up to 0.1 mm/yr in sandy sludge.
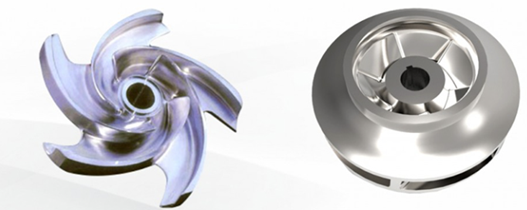
- Inspect/replace; hardface coatings.
Prevention: Material upgrades (e.g., CD4MCu duplex SS).
12. Air Binding/Air Locks
Symptoms: No flow, sputtering discharge.
Causes: Trapped air in casing/suction, common in chemical dosing with
gassing fluids like hypochlorite.
Technical Explanation: Air compresses, preventing priming; worsens with
volatile chemicals producing vapors.
- Vent/prime; install auto-vent valves; for chemicals, use degassing heads.
Prevention: Self-priming designs; foot valves; short suction lines.
13. Electrical Failures
Symptoms: Won't start, intermittent operation.
Causes: Wiring faults, surges, control panel issues.
Technical Explanation: Surges spike voltage >20%; panels fail from moisture.
- Inspect wiring; reset breakers.
Prevention: Surge protectors; NEMA 4X enclosures.
14. Bearing Failure
Symptoms: Noise, heat, vibration.
Causes: Poor lubrication, misalignment.
Technical Explanation: 50% of breakdowns; spalling from fatigue.
- Lubricate/replace.
Prevention: Greasing schedules; condition monitoring.
15. Corrosion
Symptoms: Pitting, leaks, weakened parts.
Causes: Low pH, chemicals in wastewater; accelerated in dosing pumps
with acids/bases.
Technical Explanation: Galvanic corrosion in mixed metals; rates double
per 10°C / 18°F rise.
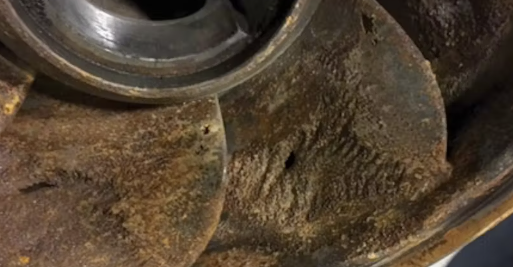
- Replace with resistant materials (e.g., PVDF for acids).
Prevention: Coatings (epoxy); cathodic protection; compatibility checks.
16. Pump Won't Turn Off
Symptoms: Continuous running, high bills.
Causes: Faulty float/control.
Technical Explanation: Stuck switches cause dry run damage.
- Inspect/replace switch.
Prevention: Redundant controls.
17. High-Level Alarm Sounding
Symptoms: Alarm triggers, rising levels.
Causes: Pump failure/overload.
Technical Explanation: Indicates wet well overflow risk.
- Shut off; diagnose underlying issue.
Prevention: Alarm testing; backup pumps.
18. Bad Smells
Symptoms: Odors from pump.
Causes: Stagnant water, mold, poor seals.
Technical Explanation: Anaerobic bacteria produce H2S.
- Clean/flush; seal checks.
Prevention: Circulation; ventilation.
19. Inconsistent Dosing/Flow in Chemical Pumps
Symptoms: Uneven chemical delivery, process inefficiencies, fluctuating
pH or treatment levels.
Causes: Air leaks in suction, clogged filters/strainers, worn
diaphragms/valves, high viscosity or bubbly fluids, incorrect calibration.
Technical Explanation: Metering pumps rely on precise stroke volume; inconsistencies
shift from BEP, reducing accuracy to <95%. In electromagnetic types, impurities block
flow paths.
- Inspect suction for leaks/blockages; clean filters; replace worn diaphragms (every 6-12 months).
- Calibrate using graduated cylinder; reduce viscosity with dilution if >500 cP.
Prevention: Regular calibration (monthly); use anti-siphon valves; monitor with flow sensors.
20. Vapor Lock in Chemical Dosing Pumps
Symptoms: Loss of prime, no flow despite running, sputtering output.
Causes: Gassing chemicals (e.g., sodium hypochlorite) producing vapors;
high temperatures; long suction lines.
Technical Explanation: Vapors accumulate in pump head, compressing instead
of pumping liquid; worsens with off-gassing rates >5% in hypo solutions.
- Install degassing valves or heads; prime manually; shorten suction lines (<5 ft).
- Cool storage tanks (<30°C / 86°F).
Prevention: Select self-degassing pumps; store chemicals properly; automatic priming cycles.
21. Diaphragm Failure in Dosing Pumps
Symptoms: Leaks, reduced output, unusual noises; chemical exposure
risks.
Causes: Overpressure, chemical incompatibility, fatigue from cycles
(>1 million), abrasives/crystallization.
Technical Explanation: Diaphragms flex 100-200 times/min; failures rupture
at stresses > yield strength (e.g., PTFE: 20 MPa), allowing backflow or leaks.
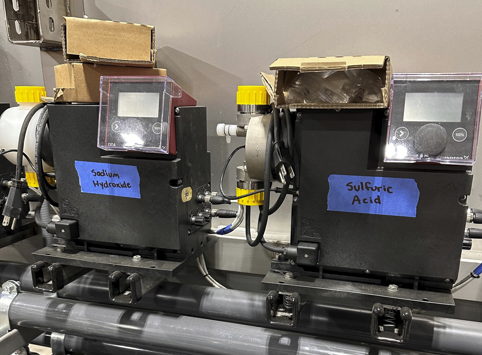
- Replace diaphragm; check pressure relief valves; verify material compatibility (e.g., EPDM for bases).
- Flush system to remove crystals.
Prevention: Pressure limits (e.g., <150 psi); routine inspections (quarterly); use multi-layer diaphragms.
22. Calibration and Control Issues
Symptoms: Over/under dosing, inconsistent treatment, alarms for
pH/chlorine levels.
Causes: Drift from wear, electrical faults (fuses, wiring), sensor
miscalibration, fluctuating pressures.
Technical Explanation: Stroke length/speed controls volume; errors cause
±10% variance, affecting stoichiometry in reactions like coagulation.
- Recalibrate with flow meter; inspect/replace fuses; secure wiring.
- Stabilize pressure with regulators.
Prevention: Automated calibration; surge protection; integrate with SCADA for real-time monitoring.
23. Siphoning/Overdosing in Chemical Pumps
Symptoms: Excess chemical use, downstream contamination, high costs.
Causes: Low discharge pressure, no anti-siphon valve, high pump
settings, rich solutions.
Technical Explanation: Gravity or pressure differential pulls extra fluid;
exceeds intended dose by 20-50% without backpressure.
- Install anti-siphon/backpressure valves; dilute solutions; adjust settings.
- Check for siphon breaks.
Prevention: Design with positive head; use injection check valves; regular audits of dose rates.
Acronyms
- API: American Petroleum Institute
- ASME: American Society of Mechanical Engineers
- BEP: Best Efficiency Point
- CD4MCu: Cast Duplex Stainless Steel Alloy 4A Modified with Copper
- cP: Centipoise
- dB: Decibel
- EPDM: Ethylene Propylene Diene Monomer
- FFT: Fast Fourier Transform
- FLA: Full Load Amperes
- H2S: Hydrogen Sulfide
- IP: Ingress Protection
- IR: Infrared
- ISO: International Organization for Standardization
- L10: Basic Bearing Rating Life
- MΩ: Megaohm
- MPa: Megapascal
- MTBF: Mean Time Between Failures
- NEMA: National Electrical Manufacturers Association
- NPSHa: Net Positive Suction Head Available
- NPSHr: Net Positive Suction Head Required
- pH: Potential of Hydrogen
- psi: Pounds per Square Inch
- PTFE: Polytetrafluoroethylene
- PVDF: Polyvinylidene Fluoride
- RMS: Root Mean Square
- SCADA: Supervisory Control and Data Acquisition
- SS: Stainless Steel
- VFD: Variable Frequency Drive
- WWTP: Wastewater Treatment Plant
FAQ Section
What are the main causes of clogging in sewage pumps?
Clogging often results from rags, wipes, grease, or debris accumulating in the impeller or pipes. Prevention includes installing upstream grinders and educating on proper disposal.
How can I prevent cavitation in centrifugal pumps?
Ensure sufficient NPSHa by increasing suction head, reducing pump speed with a VFD, or using larger suction piping. Regular monitoring of suction pressure is key.
Why does my submersible pump overheat?
Common causes include dry running, blockages, or poor ventilation. Check fluid levels and install thermal protectors for prevention.
What should I do if my pump won't start?
Inspect power sources, wiring, and control panels for faults. For float switches, clean debris or replace if malfunctioning.
How often should I maintain wastewater pump stations?
Quarterly inspections are recommended, but frequency depends on usage—busy stations may need monthly checks for clogs and wear.
What is the difference between a sewage pump and a grinder pump?
Sewage pumps pass solids without grinding, while grinder pumps macerate debris to prevent clogs in smaller pipes.
How do I fix leaks in chemical dosing pumps?
Replace worn seals with compatible materials like Viton and implement double seals. Routine ultrasonic leak detection helps.
What causes vibration in pumps, and how to remedy it?
Misalignment, imbalance, or worn bearings are common. Use laser alignment and vibration analyzers for fixes, per ISO 10816 standards.
Why is my chemical dosing pump inconsistently delivering flow?
Air leaks, clogged filters, or calibration drift may be at fault. Recalibrate monthly and use anti-siphon valves.
How can I avoid vapor lock in hypochlorite dosing pumps?
Install degassing valves, shorten suction lines, and cool storage tanks below 30°C / 86°F.
Bibliography
- Hydraulic Institute: Pump FAQs and Standards (pumps.org)
- American Petroleum Institute (API): Seal Plans and Standards (api.org)
- International Organization for Standardization (ISO): Vibration Standards (iso.org)
- American Society of Mechanical Engineers (ASME): Piping Codes (asme.org)
- National Electrical Manufacturers Association (NEMA): Enclosure Ratings (nema.org)
Would you like help with your Plant?
Contact Ecologix Environmental Systems today to learn more about our wastewater treatment solutions.
678-514-2100 Request a Consultation